Advances In Pipeline Inspection Technology: A Look At The Non-Contact Magnetometry Technology
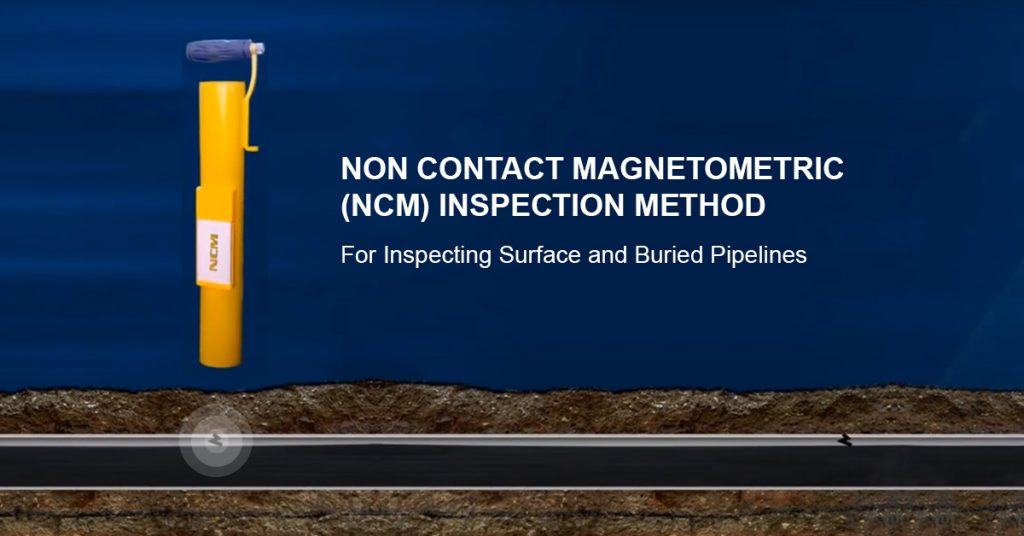
The pipelines that are used in transporting crude oil and petroleum products are often installed in adverse environments and subjected to varying operational conditions that frequently expose them to deterioration, mainly in the form of corrosion.
Such pipelines are also vulnerable to third party damage and manufacturing flaws that can cause operational challenges and loss of revenue.
Pipelines need to be secure, well-maintained, and reliable to ensure the smooth and uninterrupted flow of petroleum products from source to destination. To this end, operators should be conscious of pipeline deterioration factors so that incidences of unplanned shutdowns and leaks with environmental and economic consequences can be effectively mitigated.
One way to guarantee the safety and reliability of pipelines is to perform periodic inspections to identify damage and flaws early enough before they become serious causes for concern. There are several non-destructive testing methods for pipeline inspection, and the choice of inspection method depends on several factors that include cost, safety, reliability, availability of technical know-how, production impact, user and environmental friendliness, and operational needs.
One innovative pipeline inspection method that stands out from the numerous options is the Non-Contact Magnetometry (NCM) method, which allows for rapid assessment of buried pipelines without contact, especially when such lines are considered unpiggable.
NCM works by identifying changes along a pipeline’s magnetic field that are caused by stress, tension or corrosion. The received data is visualized in real-time and shows the locations of anomalies along the pipe, complete with GPS coordinates.
The types of anomalies that are definable by the NCM method include corrosion fatigue, weld defects, metal loss, stress-induced deformation, changes in pipeline geometry and localized damage such as pitting.
The uniqueness of the NCM technology lies in its ability to provide quick insights into the condition of buried pipes without requiring excavation, without requiring contact with the pipes, and with no production downtime.
NCM can easily be deployed onshore and can also be deployed subsea by a diver or mounted on an ROV. The NCM device is lightweight, and it is rated for a water depth of 2000m.